Quality problems caused by TIMKEN bearing heat processing method
By ballbearings
@ballbearings (236)
Nanjing, China
November 27, 2013 11:35pm CST
According to the sales experience found many clients as long as the quality of bearing surface brightness is good, this is wrong. Light should be on the surface of the bearing is a kind of raven, of the cause of the raven is whether used by TIMKEN bearing steel standard and its cutting fluid used in the grinding process and etc, produced by the two before.
Bearing the chamfer does not determine the quality of the bearing, but it reflects the bearing processing method. Chamfering is black, the heat treatment such as quenching, such increase the hardness of TIMKEN bearings, and some people think the chamfering is black not good-looking is not process completely, this is a myth.
A cage is better than two body, although the new process using one cage, but it is just to save material, and performance than the difference between the two bodies such as the rotary.
Quenching temperature is low or poor cooling will generate more than standard stipulated in the microstructure of austenite organization, called owe hot organization, it decreased hardness, wear resistance sharply reduced, affecting TIMKEN bearing life
Bearing parts in the process of hardening cooling by internal stress of crack according to quenching crack. Of the cause of the crack are: due to quenching heating temperature is too high or cooling, the thermal stress and quality of metal volume change of the organization stress is greater than the fracture strength of steel; The original defects on the surface of the work (such as surface microcrack or scratches) or steel internal defects such as slag, severe non-metallic inclusions, white spots, shrinkage residual, etc.) during quenching form stress concentration; Serious surface decarbonization and carbide segregation; Parts hardening after tempering lack or not timely temper; The previous process caused by salt stress, cold forging folding, deep turning tool and the oil groove sharp edges, etc. In conclusion, the causes of quenching crack could be one or more of the above factors, the existence of internal stress is the main reason for the formation of quenching cracks. Quenching crack deep and long, fracture surface is flat, the broken section without oxidation color. It's on the TIMKEN bearing ring is often on the longitudinal straight crack or annular crack; On the bearing steel ball shape with s-shaped, T or ring. The characteristics of the quenching crack is crack on both sides without decarburization phenomenon, with obvious difference between crack forging cracks and materials.
Bearing parts in heat treatment, there is the thermal stress and organization stress, the internal stress can overlay or partially offset each other, is complex and changeable, because it can as the heating temperature, heating rate, cooling, cooling speed, parts of the change of the shape and size changes, so the heat treatment deformation is inevitable. Know and grasp its change law can make the deformation of the bearing parts, such as ring elliptic, large size up, etc.) in a controllable scope, is advantageous to the production. , of course, in the process of heat treatment, mechanical collision also can make parts deformation, but the deformation is can be used to improve operation to reduce or avoid.
Bearing parts in the process of heat treatment, if they are in oxidizing medium heat, surface oxidation happens to make the surface of carbon mass fraction decreases, causing surface decarburization. The depth of the surface decarburization layer over the last machining allowance can make the parts scrap. The determination of surface decarburization layer depth is available in the metallographic examination metallography and microhardness method. The surface microhardness distribution curve measurement shall prevail, to do the arbitration criterion.
Caused by a lack of heating, cooling, quenching causes such as improper operation of the surface of the bearing parts local hardness insufficient phenomenon known as quenching soft point. It can cause surface to surface decarburization abrasion resistance and fatigue strength of serious decline.
Used to adjust the main factor is the installation, use and maintenance, maintenance, such as conform to technical requirements. Installation conditions is one of the factors of using TIMKEN bearing is often caused by incorrect installation package state changes between each part of the primary factor of bearing capacity, the abnormal state of operation and early failure. According to the installation of the rolling bearing, use, maintenance, maintenance of the technical requirements of operation of the rolling bearing contact load, speed, temperature, vibration, noise and lubrication condition monitoring and inspection, found that abnormal immediately to find the reason, adjust back to normal.
Rolling bearing materials is the main factor influencing the quality of metallurgy rolling bearing early failure. With the progress of metallurgical technology (such as rolling bearing steel, vacuum degassing, etc.), improve the quality of the raw materials. The proportion of raw materials quality factors in the analysis of the rolling bearing is markedly reduced, but it is still one of the main factors of TIMKEN bearing failure. Choose proper remains of rolling bearing fault analysis must be considered.
1 response
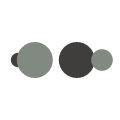