Four airlines together to create 3D printing technology
By tony smith
@guoke512 (5)
Chicago, Illinois
July 15, 2013 10:15pm CST
Over the past year, is one of the most popular trends in 3D (three dimensional) printing technology development and diffusion. Many companies now use 3D printers, through the accumulation of layers of metal powder to form a complete product or component.
The Massachusetts Institute of Technology, said General Electric Company recently used 3D printing technology to print for the new aircraft fuel nozzles. Importance: This technology can reduce the cost of manufacturing complex parts, therefore, is expected to make a lot of manufacturing revitalized.
Breakthrough: the world's largest manufacturer of General Electric Company (GE) will use 3D printing technology to print new aircraft engine on a key component - the fuel nozzles. Key Players: General Electric Airlines (GE), EADS (EADS), United Technologies Corporation (main businesses: aerospace), Pratt & Whitney Group Corporation (the two largest U.S.
aero-engine manufacturing company First, is the world's major aviation gas turbine engine manufacturers Although people have used 3D printing technology to produce a lot of products, engineers and designers have also used it to create a lot of plastic models, but like GE Aviation, as the use of 3D printing technology mass production of this
Aluminium Magnesium Alloy powder fuel nozzle is The technology is a milestone.
Because, although consumers and small business owners, 3D printing technology is not new, but the technology is only used in manufacturing to achieve maximum business impact. GE Aviation said that this nozzle is expected late in 2015 or early 2016 to complete. Each aircraft engine needs 10-20 nozzles, therefore, in the past three years, the company needs to produce annually 25,000 nozzles.
Compared with traditional technology, GE manufactures nozzles fewer
Ferromanganese powder
materials used in new ways, thus reducing the company's cost of production; Furthermore, this method produced parts lighter, better fuel for the aircraft. Traditional technologies need to be about 20 small parts are welded together, which not only takes a lot of manpower, will leave a lot of waste.
The new methods are used to manufacture such a cobalt-chromium powder parts - a computer controlled laser towards these powders precise laser beam, a electrolytic manganese powder melt in the right place, a plurality of manufacturing a layer of 20 microns thick. Because the laser can not stop work, so the new method is faster. Moreover, the new technology of the material utilization efficiency is also higher.
GE's engineers began to explore how to use 3D printing technology to produce other alloys, including some specifically designed for the 3D printer materials. For example, GE researchers are trying to airline titanium, aluminum and nickel-chromium alloys. Individual parts may be made from a variety of
Ferrochrome powder, which allow designers can not be done by casting a way tailored material properties.
For example, the engine or turbine blades can be used made of different sprayed welding alloy powder materials, therefore, be allowed to end to achieve optimal strength; while the other end can be allowed to achieve optimum heat. Now, GE's engine nozzle being tested can change 3D printing technology, high-performance products we manufacture complex way. Not only that, even had somebody wants to make 3D printing technology out of the earth into a broader space to show their glory it.
According to reports, this year in May, the U.S. space manufacturing company announced that they will work with the U.S. National Aeronautics and Space Administration Marshall Space Flight Center, is planning to use in the next year in August the United States Space Exploration Technologies Corporation cargo spacecraft, space research and development of new 3D printer sent International Space Station astronauts in orbit for production components.
By then, mankind will for the first time in the Earth's outer manufacture items. Space manufacturing company said that the international space station more than 30% of the existing spare parts are serviced by this 3D printer manufacturer. This will be an important step to the future, 3D printing technology can increase the space mission safety and reliability, while not having to transport from the Earth, can reduce the cost of space missions.
No responses
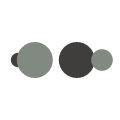