Work out new technology of high precision bearing hole
By ballbearings
@ballbearings (236)
Nanjing, China
December 26, 2013 7:41pm CST
Many indexable insert bit's problem is that they are made up of two blade cutting edges overlapping and generate the correct cutting diameter, so even if the drill bit has two clearance groove, the function of the blade is to form a single blade but asymmetric cutting edges. This design is inherently unbalanced. Indexable drills, therefore, must slow down when it enters the cutting feed speed and reduce feeding, forcing users to make a trade-off between efficiency and productivity.
Another problem is cut into the process of unbalanced bearing hole precision. Typically, indexable drills at the center of the blade cut into the first, it will produce very big radial cutting force, easy to cause drill rod deflection. Once bit off center, it can't work out high precision hole.
Because of these reasons, indexable drills are usually confined to the rough machining of holes. When the tolerance of the hole is smaller than 0.012 ~ 0.016 inches, it is necessary to increase the machining process after indexable drills.
Recently, several cutting tool manufacturers have to check again indexable insert bit, seek to overcome their inherent in the design of cutting force balance method of faults. These products in the series is one of the development of the recent Sandvik Coromant company (Fair Lawn, New Jersey) CoroDrill 880 launch. According to Sandvik product expert Bruce Carter is introduced, the design of indexable drills to avoid the problems produced by unbalanced cutting force, thus improves the productivity and the quality of the hole, while keeping the economy of the blades with four cutting edges are available. Which is the key to the company as the concept of "technology" step by step. This phrase describes the blade on the cutting edge "gradually" into the workpiece, it is said that can greatly reduce the associated with past indexable drills of radial cutting force. The concept involves two different geometric Angle of the blades and different cutting features. Center of the blade has an obvious irregular shape of cutting edge, and the outer blade is a combination of a light blade groove.
The blade in the center of the into the artifacts in the first step, the exterior Angle of contact with the workpiece. This makes bit begins with a relatively low radial force cutting, minimize the deflection of the drill pipe. In the second step, the outer blade outside contact with the workpiece. The balance the force created by the center of the blade. In the third step is the last step, the rest of the center of the blade to start cutting.
Mr Carter said, through the cutting process is divided into three relatively small steps, to reduce the cutting force is smaller than the typical blade bit processing of cutting force generated by half, and cutting force, leading to the balance between drill pipe at the entrance of the deflection is effectively eliminated. Balanced drilling in process, low radial cutting force and combination of minimizing the amount of deflection has the following benefits:
Mixer hole accuracy is higher.
The feasibility of mixer feeding has increased to 100%, depending on the workpiece material.
Mixer in deep drilling hole diameter when four or more times and more confident.
Eliminate the possibility of subsequent machining requirements, depends on the accuracy requirement.
Mentioned another advantage is that the design makes the outer blade has four completely available cutting edges. If feeding is higher than 0.005 ipr, some equipped with side blade indexable drills will loss the fourth cutting edges. But the technology step by step, the center of the different blade shape can be in feeding up to 0.013 ipr can still protect the cutting edge.
Finally, points out that Mr Carter blade on the use of light to the outer edge technology can generate good surface roughness, with this new design even higher feeding. In the experiment, when the feed is 0.004 ipr micro surface roughness can be up to 20 inches (equal to one over one million of an inch). And when feeding up to the surface roughness can reach 80 to 80 inches
No responses
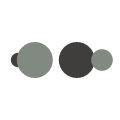