Know the core differences between through-hole and SMT techniques
By Jenny B
@pcbassemblydepot (23)
Morganton, North Carolina
February 3, 2014 1:30am CST
In the last few decades, SMT, which is one of the latest technologies for assembling electronic components, has gained a huge popularity, replacing the earlier through-hole technique. Although latter one is still being used, but surface mounting has changed the way assembling used to be done.
In this section, we will learn why this new technique has gained so much popularity and what those applications are, where through-hole mounting is still applicable. Upon gaining a little understanding of both these procedures, you will get to know about their unique characteristics and the core differences among them.
Through-hole technology
Through hole assembly technique was the popular method that was used for constructing almost all forms of PCBs (printed circuit boards). It is basically a mounting procedure that makes use of leads which are embedded on components by inserting them into holes which are drilled in PCBs and soldered into pads which are situated on the other side.
This method is extremely dependable because of the reason that if offers a sturdy mechanical bond. However, what makes it more expensive that its counterpart technique is that fact that it requires drilling of holes which makes the entire production longer and costlier.
In addition, it also creates some limitations due to presence of holes on the board. It limits the routing areas for tracking signals on the layer beneath the top layer. These are the two major issues which were solved by SMT and this is what made it a preferred choice since 1980s.
SMT (surface mounting)
Instead of manufactures having to drill holes on the board, SMT now enables them to mount the required electrical components by directly placing them on the PCB surface. Apart from this amazing benefit, the components which are used in this technique are small in terms of size compared to its counterparts.
The reason why component size is smaller is because the components usually don’t have any leads, and even if there are leads, they are very small. Surface mount devices and PCBs do not require manufacturers to drill so many holes, and come with very compact size components. This creates enough room for high density circuits on small boards.
This feature is particularly benefitting in the present day electronics industry which is becoming more complicated and compact with each day passing. Besides all these, SMT is more inexpensive than through-hole.
No responses
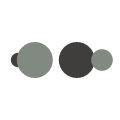