Welding metal underwater - How do they do it?
By jnr1234
@jnr1234 (129)
Malaysia
January 8, 2007 6:56am CST
I found this articles on "How Do They Do It?" 1991 book.
Just want to share with you!Welding is the fastest and cheapest way of making a repair underwater. in the past, damaged oil platforms or pipelines had to be brought to the surface before they could be mended. Now divers can weld at depths up to 100Oft (300m), but it can be dangerous and difficult.
Welding works by generating heat intense enough to fuse metals together. There are several ways of providing the heat to melt the metal, but only one of them - electric arc welding - can be used underwater.
By using a strong electric current an electrical discharge, or arc, can be made to cross a small gap between two electrodes. in the case of welding, the charge travels from an electrode at the end of a cable to the metal which needs repairing and in effect is the other electrode. The heat produced by the charge has to be sufficient to melt the metal.
People have known that welding underwater was possible since 1802 when the British scientist Sir Humphry Davy discovered that an electric charge would arc underwater. But although the method was used to temporarily repair ships in the Second World War, it has only been widely used since the 1970s, when an increasing number of under-water repairs needed to be carried out on oil platforms and pipelines.
1 There are two different sorts of underwater welding. The simplest method is ‘wet water’ welding, for which a generator on the surface provides a large current of about 500amps which is fed through an insulated cable to the diver who does the welding. To prevent the current ‘leaking’ into the water and becoming weaker, the electrodes are coated with wax or waterproof paint.
The major problem with wet water welding is that the water cools the metal being welded very quickly, which makes the weld hard but also very brittle. Oxygen and hydrogen gas, produced from the water by the heat of the weld, penetrate the weld when it is hot, which can weaken it further. Another limitation of wet water welding is that it cannot be carried out at depths of more than 30Oft (90m), because the pressure of the water becomes too great for the electric charge to arc.
The second method of underwater welding - dry chamber welding - can be used at greater depths and also produces better quality welds, but it is expensive.
First, the area that needs repairing is surrounded with a tough, transparent plastic jacket or box. Then the water is displaced by blowing compressed gas into the box so that the area of metal around the weld is dry.
The bottom of the chamber is open, so the diver can reach inside to use the welding torch. The gas trapped inside the box prevents the water getting in. Divers sometimes have difficulty seeing how their work is progressing because smoke and steam generated by the weld can obscure their view.
Even more ambitious welds can be carried out by surrounding the whole area with a high-pressure chamber large enough to accommodate the diver as well. This produces better results, comparable with welds above the surface, but it is expensive because the chambers usually have to be specially designed to fit over the area of pipeline or joint which needs repair and costly seals have to be made. At least one support ship is needed, together with a barge crane to raise and lower the chamber.
Some of the largest chambers have room for several divers to work and even rest between shifts. They have been used at depths of 1000ft (300m) or more.
With oil companies drilling deeper and deeper, there is a need for underwater welding at anything up to 2000ft (600m). Engineers believe this will soon be possible using the dry chamber technique. But for welding at such great depths it is likely that divers will be replaced by remote-controlled robots.
I wonder if there is any other ways. Are they?
No responses
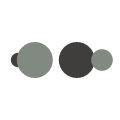